👋 Introduction: When Will We Learn?
Let’s call this out from the start.
You’ve got tap diffusers contaminated with Pseudomonas, smothered in limescale, and riddled with biofilm.You’re now in the process of replacing them — again. But you’re replacing them with… the exact same type of diffuser?
Why?
Honestly — why would you do that?
We’ve all heard the line:
“The definition of madness is doing the same thing over and over and expecting a different result.”
And here we are, in healthcare environments across the UK, doing just that. Swapping like-for-like and hoping for a different outcome.
It’s not just a missed opportunity — it’s a safety risk and a waste of money.
🚿 The Usual Suspects: Limescale, Biofilm & Pseudomonas
Let’s talk about what’s really going on.
Every time you unscrew a contaminated diffuser, you’re looking at three enemies:
-
Limescale – the perfect foundation for biofilm to form.
-
Biofilm – sticky, shielded, and home to pathogens.
-
Pseudomonas aeruginosa – opportunistic, antibiotic-resistant, and absolutely not welcome in healthcare settings.
They thrive inside traditional diffusers, especially in environments where outlets aren’t flushed regularly or cleaning is inconsistent. Worse still, most tap ends are impossible to clean thoroughly — especially when you factor in calcification and stubborn deposits.
And it’s not just the bugs that pose a problem — it’s the way the water flows.
Old-style diffusers encourage backflow, cross-contamination, and retention of stagnant water — all things you don’t want in a clinical environment. Even when you manage to clean them, you’re often just polishing the surface of a deeper issue.
So why, in 2025, are we still reinstalling the very same components that allowed all of this to happen?
🧠 A Moment of Clarity: Time for Better Thinking
If your current solution leads to repeated contamination, the solution isn’t maintenance.
The solution is replacement with something better.
Not just different — better. Safer. Smarter. Designed for purpose.
Which brings us to something game-changing.
🔒 Meet the Game Changer: The Patented Sentinel Tap Valve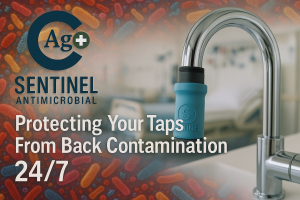
Let’s pause here. What if you could:
✅ Eliminate the risk of mechanical backflow
✅ Create a permanent, impenetrable anti-microbial barrier
✅ Stop biofilm forming before it even begins
✅ Avoid limescale build-up in the first place
✅ And do all of that with one simple component?
Well, you can.
The Sentinel Tap Valve isn’t just a diffuser — it’s a barrier, a filter, a cleaner, and a guardian all rolled into one.With three integrated levels of protection, it rewrites the rulebook on tap-end safety.
🛡️ The Three Layers of Protection Explained
1. Anti-Microbial Protection (24/7)
The Sentinel valve is built with integrated anti-microbial material — not coated, not dipped, but part of the very body of the component. That means the moment any water or pathogen comes into contact with it, the protection is already at work.
This protection is ongoing. It doesn’t wash off. It doesn’t need reapplying. It’s always on.
2. Mechanical Backflow Prevention
No more hidden risks or guesswork. This valve physically prevents water from flowing back up the tap — meaning bacteria, biofilm, or debris in the system downstream can’t make its way back in. Cross-contamination? Blocked at the source.
3. Anti-Microbial Barrier That’s Impenetrable
We’re talking about a physical and microbial fortress. This barrier is clinically designed to keep contaminants out — and even more impressively, it keeps calcification and fouling to a bare minimum.
In short: It’s not just cleaner. It stays clean.
🧼 Easy to Clean, Easy to Maintain
With traditional diffusers, maintenance is frustrating and often a false economy. Trying to clean around scale and inside crevices, only for biofilm to recolonise within days, is a waste of staff time and budget.
The Sentinel Valve’s smooth design prevents calcification, and when cleaning is needed, it takes seconds — not hours. No need for vinegar soaks, aggressive descaling chemicals, or complex removal.
If it’s easier to maintain, it’s more likely to be maintained — and that translates to fewer issues, fewer call-outs, and fewer outbreaks.
🧾 But What About Cost?
Let’s address this head-on.
Yes, a Sentinel Tap Valve cost is slightly more as it initially comes with a selection of adaptors which you will not need on subsequent changes which will bring costs down even further. But compare that against:
-
Time spent deep-cleaning traditional tap ends
-
Risk of tap failure due to limescale build-up
-
Cost of patient infections or isolation protocols
-
Emergency flushing procedures
-
Negative audit findings
-
Staff disruption
-
Negative press or reputation damage
In every measurable way, the Sentinel saves you money.
It’s not just a tap-end upgrade — it’s a strategic infection control decision.
🔁 Break the Cycle
Let’s get real. If your estates team is already planning the next round of tap-end replacements, ask one thing:
“Are we solving a problem- or just repeating the cycle?”
If the answer is “we’ve always done it this way,” it’s time to challenge that thinking.
You don’t need to replace your diffusers with something identical.
You need to replace them with something intelligent.
💬 Real Talk from the Field
“We used to change diffusers every few months. With Sentinel, it’s once
— and we don’t look back.”— NHS Estates Manager, Midlands
“Pseudomonas was a constant headache. Since moving to Sentinel, we’ve seen zero failures in 18 months.”— Infection Control Lead, London Trust
“Our tap ends used to be the weak point. Now they’re the strongest part of our water safety plan.”— DIPC, NHS Foundation Trust